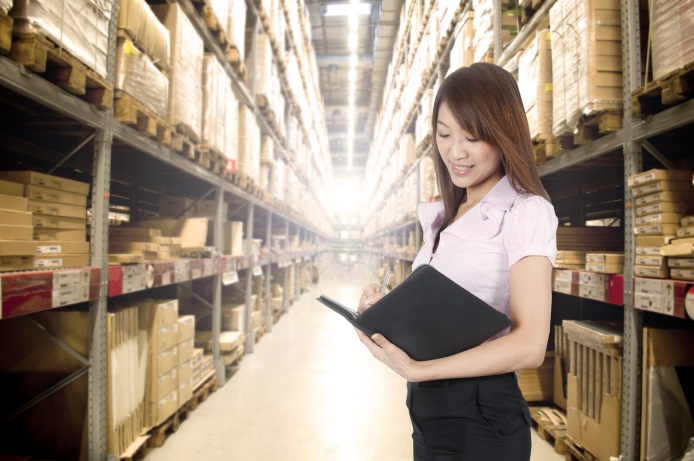
Unfortunately, most order completion errors take place in the warehouse, and these types of mistakes are the ones that can critically affect your business. These errors cost time and sometimes large amounts of money and can cripple your repeat business and may result in negative customer reviews.
If orders are ultimately incorrect or incomplete after they leave the warehouse, everything else that you do to boost your company’s reputation and sales means little. Warehouse shipping solutions are essential to the overall success of your business endeavors. Follow these tips to help your warehouse stay profitable.
Adequately Train Your Employees
Automated systems work, but only to a certain point. Ultimately, people ensure the accuracy of a particular shipment, so it’s in your best interest to see that they have the tools and training that they need to do the job.
Invest in training modules and workshops, so your warehouse employees feel confident in their skills. Identify which employees succeed, and in which areas of the workflow, and assign their stations accordingly. Your warehouse team is only as strong as your weakest employee, so it’s important you know where the team’s strengths lie.
Many warehouses offer incentives to employees who maintain quality control, and this can work wonders for accuracy. Set a goal for your employees, and ask them to meet it biweekly or monthly. Ask for a certain level of order and cleanliness to be maintained in the warehouse, and reward those employees who are on task. While incentive programs may seem juvenile, they consistently work.
Verify, Then Verify Again
Though people are the most effective means of ensuring accuracy, human error is the leading cause of incorrect shipments, so it’s important that each order is verified by a human before it leaves the warehouse. Keep careful track of your shipment error rate; know the numbers by heart, and where in the flow the errors are taking place so you can take measures to correct errors.
Order pickers need to be carefully monitored. Be sure you as a supervisor know which pickers are racking up the largest number of mistakes, and make sure that the employee knows as well. Encourage them to double check each and every order before they send it through the workflow.
As many warehouse pickers also do their own quality control, it may be wise to add an independent employee to the roster. Order pickers may not always adequately check their own work, and another person in the supply line might be better suited to perform that task.
Manage Inventory
For the best order accuracy it’s essential you maintain adequate inventory stock and ensure the inventory records are verified. While many errors occur during the picking process, an equal or greater number occur in the inventory department.
Make sure that those who are responsible for receiving are accurately verifying and counting each shipment. Make sure that the employees responsible for putting away and shelving each incoming shipment are recounting and verifying the orders as well. Additionally, the data entry department needs to be held accountable for their role in inventory.
Each department has some level of impact on the accuracy of the entire workflow, and it’s important they all work together and hold themselves and each other accountable.
Know Your Shipping Company
Each company probably has a preferred shipping vendor, but it’s important to know your provider is the best that you can do for your customers. Securing the best shipping rate is instrumental in keeping your costs down, but are you ultimately hurting your bottom line in the process?
Many companies swear by the United States Postal Service, and others prefer private shipping services like UPS or FedEx. The benefits of using FedEx or UPS over the USPS can come down to something as simple as proof of delivery. The USPS doesn’t always provide this service, which can directly impact your records and the customer’s purchase.
Additionally, the USPS often won’t deliver directly to warehouses or shipment receiving areas, opting instead to deliver to the main or front office. This can cause delays in shipment verification which affect each of your order stations in domino-like succession.
Customer satisfaction is the ultimate goal for each and every company. With more streamlined and accurate ways to manage warehouse functions and employee performance, your business can be on the fast track to increased success.