Supply chain management (SCM) is a term that has emerged in recent years that captures the essence of integrated logistics and even goes beyond it. Supply chain management emphasizes the logistics interactions that take place among the functions of marketing, logistics, and production within a firm and those interactions that take place between the legally separate firms within the product-flow channel.
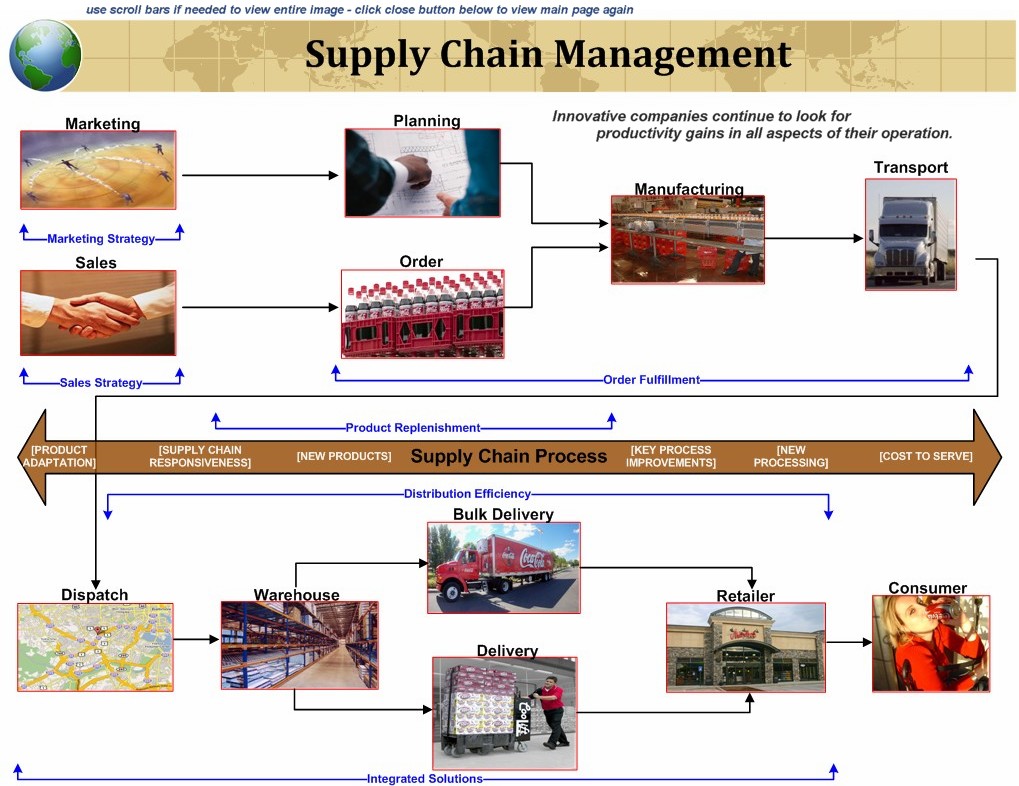
Opportunities for cost or customer service improvement are achieved through co-ordination and collaboration among the channel members where some essential supply chain activities may not be under the direct control of the logistician. Although early definitions such as physical distribution, materials management, industrial logistics and channel management - all terms used to describe logistics - have promoted this broad scope for logistics, there was little attempt to implement logistics beyond a company’s own enterprise boundaries, or even beyond its own internal logistics function. Now, retail firms are showing success in sharing information with suppliers, who in turn agree to maintain and manage inventories on retailers’ shelves.
Channel inventories and product stockouts are lower. Manufacturing firms operating under just-in-time production scheduling build relationships with suppliers for the benefit of both companies by reducing inventories. Definitions of the supply chain and supply chain management reflecting this broader scope are: “The supply chain (SC) encompasses all activities associated with the flow and transformation of goods from the raw materials stage (extraction), through to the end user, as well as the associated information flows. Materials and information flow both up and down the supply chain.”
“Supply chain management (SCM) is the integration of these activities, through improved supply chain relationships, to achieve a sustainable competitive advantage.” After careful study of the various definitions being offered, Mentzer and other writers propose the broad and rather general definition as follows: “Supply chain management is defined as the systematic, strategic coordination of the traditional business functions and the tactics across these business functions within a particular company and across businesses within the supply chain, for the purposes of improving the long-term performance of the individual companies and the supply chain as a whole.”
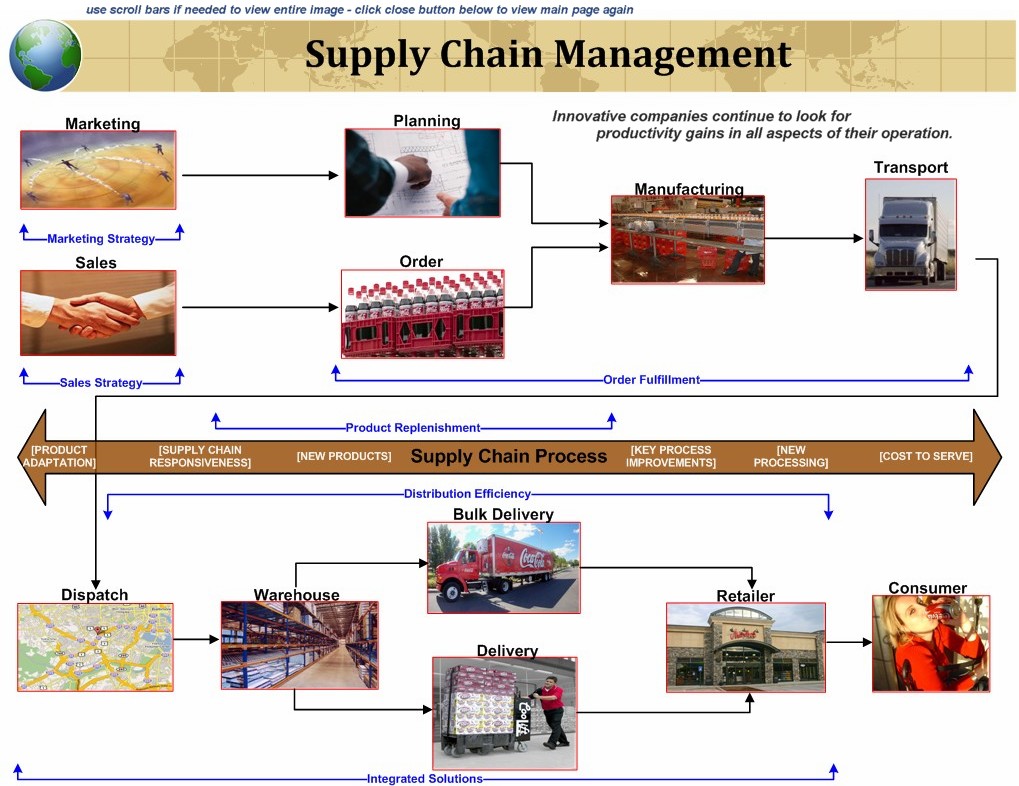
Opportunities for cost or customer service improvement are achieved through co-ordination and collaboration among the channel members where some essential supply chain activities may not be under the direct control of the logistician. Although early definitions such as physical distribution, materials management, industrial logistics and channel management - all terms used to describe logistics - have promoted this broad scope for logistics, there was little attempt to implement logistics beyond a company’s own enterprise boundaries, or even beyond its own internal logistics function. Now, retail firms are showing success in sharing information with suppliers, who in turn agree to maintain and manage inventories on retailers’ shelves.
Channel inventories and product stockouts are lower. Manufacturing firms operating under just-in-time production scheduling build relationships with suppliers for the benefit of both companies by reducing inventories. Definitions of the supply chain and supply chain management reflecting this broader scope are: “The supply chain (SC) encompasses all activities associated with the flow and transformation of goods from the raw materials stage (extraction), through to the end user, as well as the associated information flows. Materials and information flow both up and down the supply chain.”
“Supply chain management (SCM) is the integration of these activities, through improved supply chain relationships, to achieve a sustainable competitive advantage.” After careful study of the various definitions being offered, Mentzer and other writers propose the broad and rather general definition as follows: “Supply chain management is defined as the systematic, strategic coordination of the traditional business functions and the tactics across these business functions within a particular company and across businesses within the supply chain, for the purposes of improving the long-term performance of the individual companies and the supply chain as a whole.”