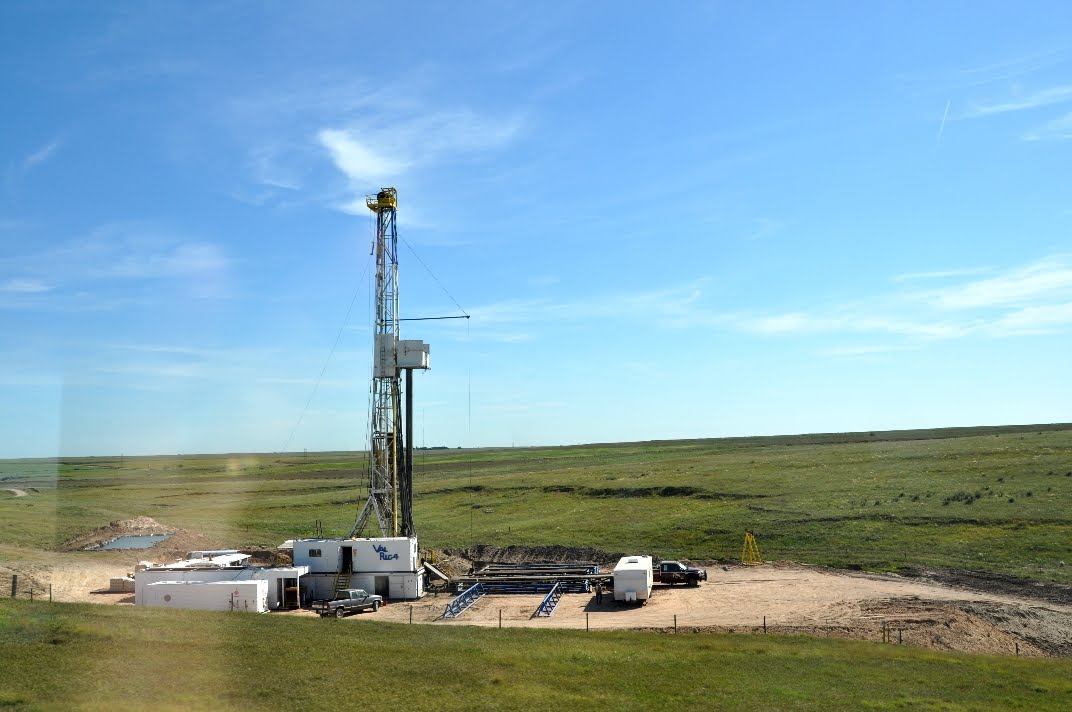
We don't need to highlight the amount of pressure generated during the oil and gas drilling process - there have been countless stories in the press of all of the problems that it can create.
Bearing the above in mind, it won't be surprising to read that perforated and fractured pipes are completely commonplace in this industry. The pressure generated means that firms are constantly having to find ways in which to repair these losses of circulation and the introduction of additives is generally the primary course of action.
Something else that won’t raise many eyebrows is the fact that there are hoards of different additives that can be used to treat this problem. Rather than cipher through all of the products that are available, we'll instead take a look at some of the factors that should be considered when deciding what type of additive to use.
Factor #1 - The hole size
The most obvious consideration to take into account is how significant the perforation size is. Unsurprisingly, there are different strengths of additives and while some holes may require one type, others may require a completely different solution.
Factor #2 - Depth of the well
The depth of the well should also be considered as it gives a decent indication of the geological stability of the area. Again, some additives just won't compatible with the region because they may compromise the integrity of the well due to its depth. Click here for more information about wellbore stability and the types of additives that can be utilised.
Factor #3 - The nozzle size of the drill
Considering the fact that the additive is affecting the deeper areas of the well, a lot of people are surprised to see that the nozzle has an influence on what additive is chosen. However, the make-up of some additives is much different to others and this can mean that some are much thicker. It's in these instances where the drill size is particularly crucial, as the thicker solutions just won't be able to pass through it. As such, one could say that this is the first issue to tackle, just to cancel out the additives that cannot be used.
It's not all related to the drill nozzle though, with other elements of the equipment also determining just what type of additive can be used. For example, some drill strings are not able to accommodate certain thicknesses of additive and this is something else which can influence the decision.
Factor #4 - The drilling fluid
If you have already taken a look at some additives, you'll probably be aware that some of them are compatible with different fluids. The most common type of fluid is a water-based mud, although it's also possible to utilise oil and gas based ones. Some of the more popular additives are compatible in all three, but it goes without saying that not all of them are like this so some solutions are again immediately cancelled out.